Imagine you’re in an ancient pottery workshop, surrounded by beautifully crafted vases and bowls. The potter skillfully shapes the clay, transforming it into functional art. For thousands of years, ceramics have played a vital role in our lives, from everyday dishes to intricate sculptures. But as technology advances, so do the materials we use. Advanced ceramics—the high-tech cousins of traditional ceramics that promise to revolutionize various industries. So, what makes these advanced materials so special? Let’s dive into the world of ceramics and uncover the differences in durability between traditional and advanced ceramics.
1. What Are Traditional Ceramics?
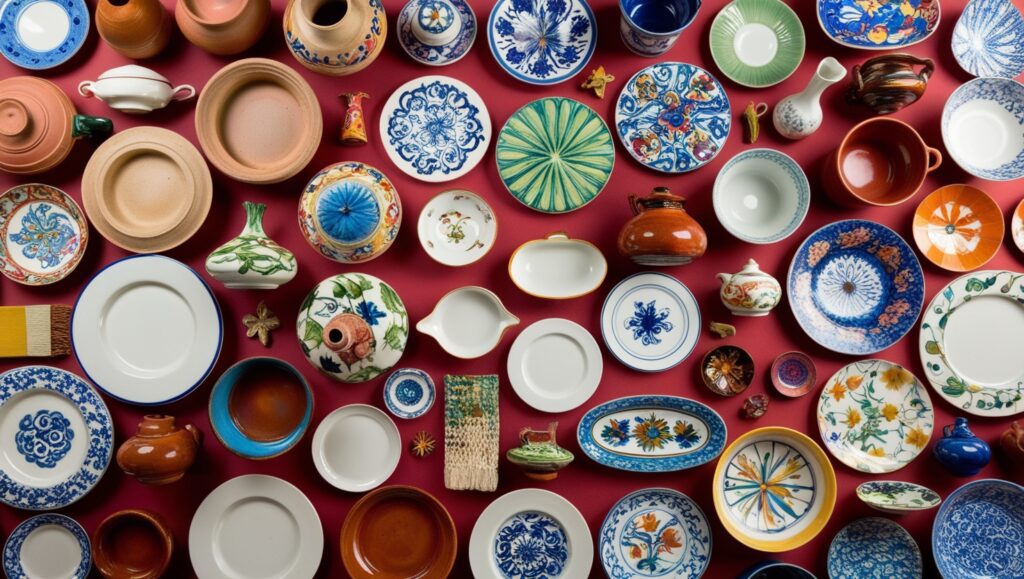
Traditional ceramics are made from natural materials like clay, feldspar, and quartz. These raw ingredients are shaped and then fired at high temperatures to create durable items. You might be familiar with common types such as earthenware, stoneware, and porcelain. While these materials are admired for their beauty and functionality in everyday items (who doesn’t love a good coffee mug?), they do have some limitations.
2. Key Characteristics of Traditional Ceramics
Brittleness: Traditional ceramics are known for being brittle. This means they can easily crack or break when subjected to stress. Picture this: you drop your favorite ceramic plate on the floor—oops! It shatters into pieces.
Lower Strength: Compared to advanced ceramics, traditional ceramics generally have lower tensile (pulling) and compressive (squeezing) strength. They can handle some pressure but aren’t ideal for heavy-duty applications.
Limited Thermal Resistance: Traditional ceramics can withstand moderate temperatures but often struggle in extreme heat or rapid temperature changes. Think about how a pizza stone can handle high temperatures while a regular ceramic plate might not fare so well in the oven.
3. What Are Advanced Ceramics?
Advanced ceramics are engineered materials designed for specific applications that require enhanced performance characteristics. They are produced using sophisticated processing techniques that allow for precise control over their properties. Common examples include alumina (Al2O3), zirconia (ZrO2), silicon carbide (SiC), and silicon nitride (Si3N4).
4. Key Characteristics of Advanced Ceramics
4.1. High Strength and Toughness:
Advanced ceramics exhibit significantly higher mechanical strength and toughness compared to traditional ceramics. For instance, zirconia is renowned for its exceptional toughness and is often used in dental implants and structural components.
4.2. High Strength and Toughness:
Advanced ceramics exhibit significantly higher mechanical strength and toughness compared to traditional ceramics. For instance, zirconia is renowned for its exceptional toughness and is often used in dental implants and structural components.
4.3. Superior Wear Resistance:
Many advanced ceramics possess excellent wear resistance, making them ideal for cutting tools, grinding media, and wear-resistant coatings—imagine tools that last longer without wearing down!
4.4. Thermal Stability:
Advanced ceramics can withstand extreme temperatures without degrading or losing their structural integrity. Silicon nitride can operate effectively at temperatures exceeding 1200 °C (2192 °F), making it suitable for high-performance applications in aerospace and automotive sectors.
5. Durability Comparison: Advanced vs. Traditional Ceramics
Now that we understand what both types of ceramics are, let’s compare their durability across several key factors:
5.1. Mechanical Strength:
-
- Advanced Ceramics: These materials typically have higher tensile and compressive strength due to their engineered microstructure. For example, zirconia is known for its exceptional toughness and is frequently used in applications requiring high durability.
- Traditional Ceramics: While some traditional ceramics like porcelain can handle compression well, they lack the tensile strength needed to withstand bending or stretching forces.
5.2. Impact Resistance:
-
- Advanced Ceramics: The toughness of advanced ceramics allows them to absorb energy better during impacts—think of them as the resilient athletes of the material world! This property is crucial for applications such as armor materials or components subjected to dynamic loads.
- Traditional Ceramics: Their brittleness makes them prone to fracture upon impact or sudden stress—like a glass ornament dropped on a hard floor.
5.3. Wear Resistance:
-
- Advanced Ceramics: Materials like silicon carbide and alumina are highly resistant to wear and abrasion, making them perfect for industrial applications where durability is paramount.
- Traditional Ceramics: While some traditional ceramic materials may provide decent wear resistance (e.g., stoneware), they generally do not match the performance of advanced ceramics in harsh environments.
5.4. Thermal Stability:
-
- Advanced Ceramics: These materials can endure high temperatures without losing structural integrity—ideal for environments where heat is a constant challenge.
- Traditional Ceramics: They may withstand moderate heat but can suffer from thermal shock or degradation when exposed to elevated temperatures.
6. Applications Highlighting Durability Differences
Let’s take a look at some real-world applications where these differences in durability come into play:
6.1. Aerospace Industry:
Advanced ceramics are crucial in turbine blades and thermal barrier coatings due to their high-temperature stability and mechanical strength. Traditional ceramics simply cannot withstand the extreme conditions present in aerospace applications.
6.2. Medical Devices:
Bioceramics like zirconia are favored for dental implants because of their durability and biocompatibility. Traditional ceramics lack the necessary mechanical properties required for such demanding medical applications.
6.3. Industrial Tools:
Cutting tools made from advanced ceramics provide superior wear resistance compared to traditional ceramic tools, resulting in longer service life and enhanced performance during machining processes.
7. Conclusion
In summary, advanced ceramics significantly outperform traditional ceramics in terms of durability due to their high mechanical strength, impact resistance, wear resistance, and thermal stability. As industries continue to seek materials that can withstand demanding conditions while maintaining performance integrity, advanced ceramics will play an increasingly vital role across various sectors—from aerospace to medical devices.
Understanding these differences empowers engineers and manufacturers to make informed decisions when selecting materials tailored for specific applications. By embracing advancements in ceramic technology, we not only enhance our capabilities but also pave the way for innovative solutions that meet modern engineering demands.
So next time you’re faced with choosing between a traditional ceramic mug or an advanced ceramic cutting tool, you’ll know exactly which one packs the punch!
8. References
- “Properties of Advanced Ceramics,” ScienceDirect. Available at: https://www.sciencedirect.com/topics/materials-science/advanced-ceramics
- “Ceramic Materials Properties,” TechTarget. Available at: https://www.techtarget.com/search/query?q=ceramic+materials
- “The Role of Advanced Ceramics in Modern Technology,” Journal of Materials Science. Available at: https://link.springer.com/article/10.1007/s10853-018-2840-8
Note: The blog is written by thoroughly referring above references, with final editing and verification by the content team. We prioritize accuracy and quality in every article.