Digital twin technology is rapidly transforming the landscape of mechanical engineering, particularly in design and manufacturing. By creating virtual replicas of physical systems, products, or processes, digital twins enable engineers to simulate real-world behaviors, optimize operations, and make informed decisions. This blog post explores how digital twins contribute to reducing production costs in mechanical engineering, focusing on their applications in product development, process optimization, and predictive maintenance.
1. Understanding Digital Twin Technology
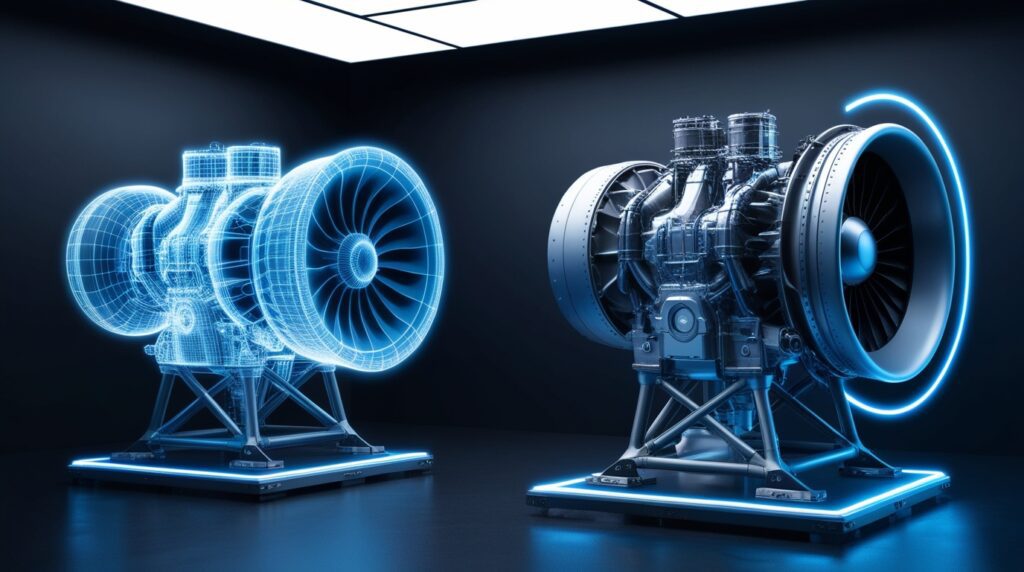
A digital twin is a dynamic digital representation of a physical object or system that uses real-time data to mirror its counterpart accurately. This technology integrates data from sensors and other sources to create a comprehensive model that evolves alongside its physical counterpart. Digital twins provide insights that help engineers understand how their designs function in real life.
2. Cost Reduction in Product Development
Digital twins are game-changers when it comes to slashing costs during product development by allowing engineers to test and perfect designs in a virtual environment.
2.1. A Safe Playground for Ideas:
With digital twins, design teams can explore endless possibilities without the hefty price tag of physical prototypes. Instead of crafting two or three preproduction prototypes, they might only need one, saving both time and resources.
2.2. Smarter Testing and Validation:
Engineers can test designs in lifelike conditions, including extreme scenarios, before they’re physically built. This means fewer expensive fixes later and more confidence in the final product.
2.3. Speeding to Market:
Companies using digital twins report development times shrinking by 20% to 50%. Faster development not only saves money but also gives a competitive edge by getting products into customers’ hands sooner.
3. Process Optimization
Digital twins are key to fine-tuning manufacturing processes, bringing significant savings and efficiency.
3.1. Eyes on the Production Line:
Real-time monitoring with digital twins helps manufacturers spot bottlenecks and inefficiencies instantly. Quick adjustments can boost productivity without halting operations.
3.2. Simulating the Perfect Workflow:
By testing different production setups in the virtual world, engineers can find the most efficient workflows, reducing waste and saving money.
3.3. Informed Decisions, Every Time:
With real-time data at their fingertips, organizations can make smarter choices that enhance output while keeping costs low.
4. Predictive Maintenance
Keeping machines running smoothly is easier and cheaper with digital twins.
4.1. Staying One Step Ahead:
Digital twins can predict equipment failures before they happen, avoiding costly breakdowns and emergency repairs.
4.2. Tailored Maintenance Plans:
By analyzing historical data, digital twins pinpoint the best times for preventive maintenance, reducing unexpected downtime and extending machine life.
5. Improved Quality Control
Ensuring top-notch product quality becomes effortless with digital twins.
5.1. Catching Issues Early:
Real-time simulations and monitoring spot defects during development, cutting down on wasted materials and rework costs.
5.2. Happier Customers:
Products created with digital twins tend to have fewer problems, leading to satisfied customers, fewer warranty claims, and stronger sales.
6. Conclusion
Digital twin technology is a powerhouse for cost reduction in mechanical engineering, transforming how we approach product development, manufacturing, maintenance, and quality control. By adopting this innovative tool, companies unlock unparalleled efficiency and savings while driving sustainability.
7. References
- McKinsey & Company – Digital Twins: The Key to Smart Product Development: [Read More](https://www.mckinsey.com/industries/industrials-and-electronics/our-insights/digital-twins-the-key-to-smart-product-development)
- Ignitiv – Digital Twins in Manufacturing: A Comprehensive Guide: [Read More](https://www.ignitiv.com/digital-twins-manufacturing/)
- https://www.insertec.biz/blog/use-of-simulation-and-digital-twins-in-the-foundry-industry/
- https://www.iom3.org/resource/digital-twins-for-high-value-components.html
- https://www.luminousxr.com/blog/what-is-a-digital-twin-in-smart-manufacturing/
- https://www.iiconsortium.org/pdf/2021_March_JoI_Digital_Twin_and_IIoT_in_Optimizing_Manufacturing_Process_and_Quality_Management_SA.pdf
- https://frigate.ai/assembly/how-digital-twins-and-smart-factories-are-revolutionizing-assembly-in-industry-4-0/
- https://www.jabil.com/blog/how-digital-twins-lead-to-manufacturing-profitability.html
- https://strathprints.strath.ac.uk/81081/1/Rahimi_etal_MW_2022_Digital_twins_for_high_value_components.pdf
- https://blog.3ds.com/industries/infrastructure-energy-materials/forging-a-sustainable-future-the-role-of-virtual-twins-in-the-steel-industry/